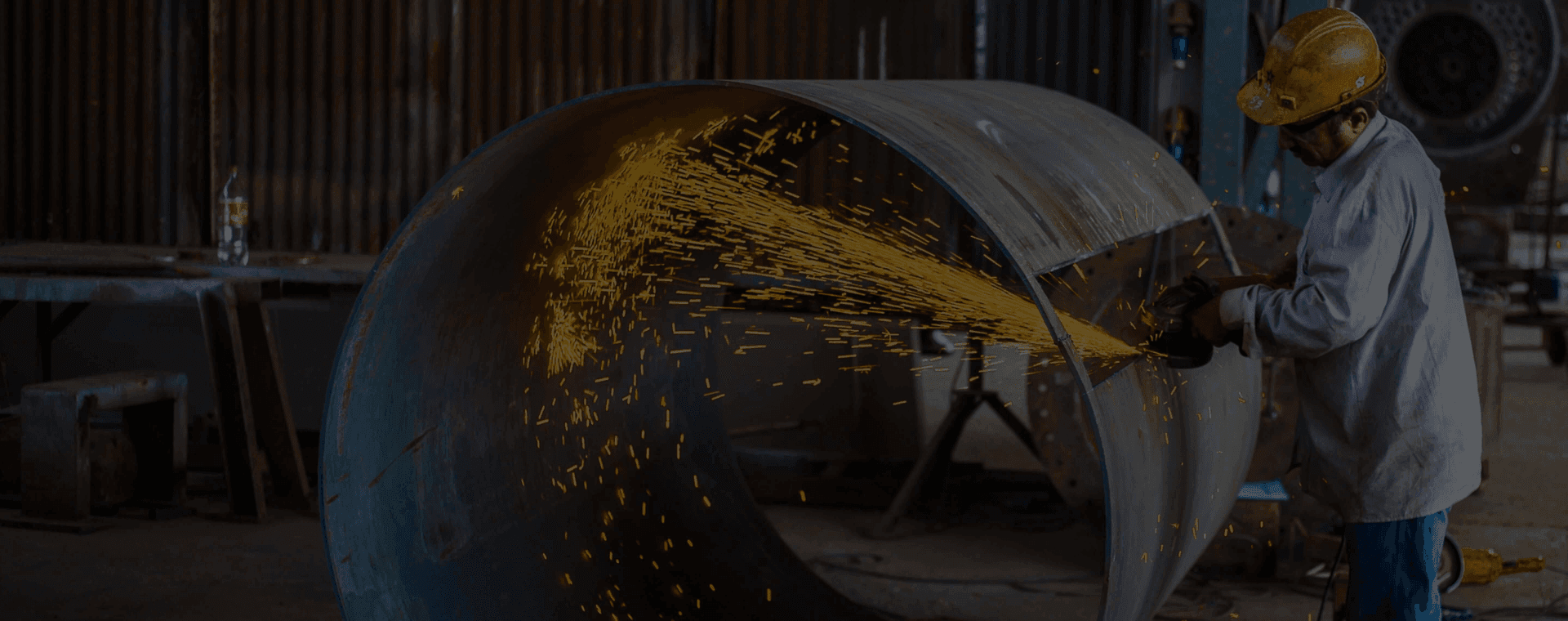
How AI Helps Monitor Thermal Anomalies in Industrial Settings
When it comes to industrial settings, safety is of utmost importance. Manufacturing environments often carry high risk. Workplace incidents, breakdowns, and fires are quite common in industry and may result in severe injuries and fatalities, lead to unplanned downtime, and cost factories billions of dollars in losses. Only through constant monitoring of machinery conditions can manufacturers minimize accident hazards to employees, make sure that equipment works at its maximum efficiency without anomalies, and take action to avert problems before they happen.
There are many parameters to monitor, among which temperature is one of the key ones. Any machinery produces heat while working, which runs the risk of failure. On the scale of an industrial setting, the results of the equipment overheating can be devastating. Industrial fires not only put human lives at risk but also cause extensive property damage and business disruption, which generally prove extremely costly.
Given that most of the time, thermal anomalies do not occur abruptly, it is crucial for manufacturers to have efficient tools in place to identify thermal anomalies before they become problems. In this article, we will explore how thermal cameras paired with AI technology can be utilized in industrial environments and what benefits AI-powered thermal screening can bring.
How thermal cameras work with AI
To put it simply, thermal cameras monitor the highest-risk areas of industrial settings, machinery, and electric equipment in the infra-red spectrum to see abnormal changes in temperature that may indicate overheating or a potential fire. AI analytics is utilized to automate detection of potential failures and allow rapid human intervention before there is a thermal runaway or fire.
Factory equipment needs regular, thorough analysis and monitoring of the overall system to prevent machine failure, reduce unplanned downtime, lower long-term maintenance costs, and improve the lifetime of industrial machines. Though periodic thermography inspections are conducted a few times throughout the year, it is often not enough as critical issues could occur in between inspections.
Using AI, it is possible to implement continuous, remote, and around-the-clock temperature control in industrial settings. AI-powered systems monitor the critical assets, analyzing the images received from thermal cameras and, if machinery overheating is detected, sending an instant alert, allowing maintenance teams to rapidly respond to the issue. Due to early problem detection, they can take suitable recovery measures and safely schedule out repairs, thus preventing the plant from breakdown and other serious consequences.
Use cases for industrial settings
AI can be utilized in a wide range of industrial environments to monitor the thermal behavior of equipment. One example is monitoring electrical components, such as cables and wiring, or inspecting electrical power systems, substations, and transformers to prevent blackouts, minimize the risk of fires, and reduce electrical equipment damage. NFPA reports that electrical distribution and lighting equipment were the leading causes of structure fires in industrial properties, accounting for 24% of the total, while heating was the leading cause of structure fires in manufacturing facilities, accounting for 15% of the total. In general, loose connections and unbalanced loads in electric power systems increase resistive heating, which can cause inflammation. Transformers often explode and burn, causing massive electrical failures, property damage, injuries, and deaths. With thermal scanning, such incidents could be prevented. AI-powered thermal screening solutions can remotely monitor electrical equipment and identify any increase in temperature, allowing operators to rapidly correct possible failure points.
Keeping track of the equipment operating temperature at manufacturing facilities is another way in which AI can be implemented. The best thing is that it enables making machinery maintenance smarter, performing timely repairs, and reducing the number of reactive maintenance scenarios.
Thermal anomaly detection can also be deployed to monitor lithium-ion batteries, which are increasingly used in the industry. Damage and incorrect handling of batteries lead to an increased risk of fire and explosion. Thermal runaway is a critical issue for energy storage batteries. A chain reaction takes less than 60 seconds from start to explosion and leads to uncontrollable fires which are difficult to extinguish by conventional means. Thermal cameras and AI analytics are used to identify problematic battery packs whose temperature reaches a critical point and allow fast intervention before internal heating gets out of hand. This helps make batteries safer, whether they are in battery packs or being transported and stored.
Leveraging AI is also instrumental for fire detection. Fire safety threats are common for manufacturing plants. According to the NFPA , US fire departments respond to an average of 37,910 industrial fires per year. Hot work such as welding or torch cutting, overloaded electrical equipment, combustible dust, and flammable liquids are just some of the most common causes of fires. Another issue is industrial dumpster fires. Fires not only risk lives but also cause serious damage to valuable assets and cost manufacturers billions of dollars ($1.2 billion per year, according to NPFA). And on top of that, industrial fires cause very high levels of pollution that adversely affect the health of people in surrounding areas, e.g. up to 5,000 times the normal concentration of benzene. In most cases, conventional fire solutions won’t detect these fires as they are not efficient outside and can detect fire only when smoke reaches sensors. Unlike conventional methods, computer vision-based solutions can detect smoke at a greater distance based on the images from thermal cameras.
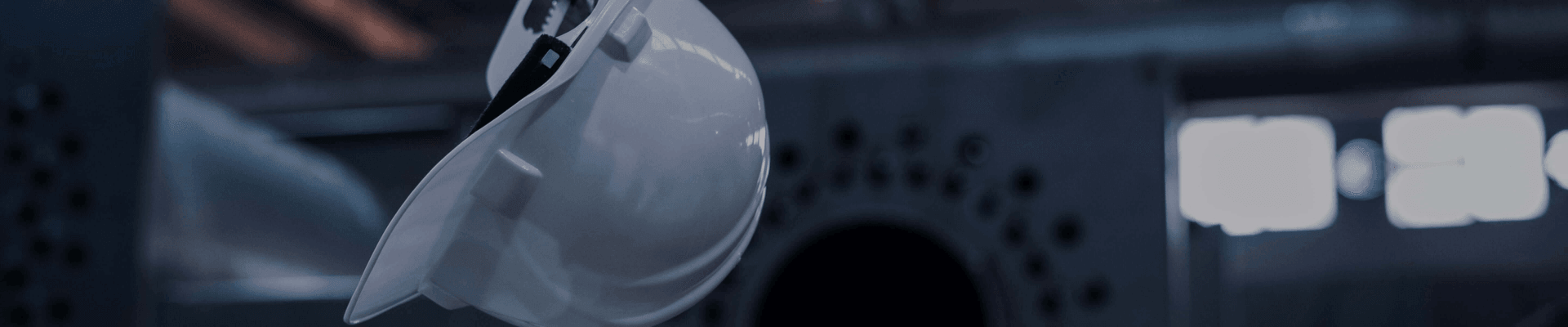
The benefits of AI-powered thermal screening in industrial settings







Final Takeaway
In industrial environments, AI analytics is now integrated with thermal cameras to implement smart temperature screening of critical equipment, infrastructure, and people. It enables reducing machinery failures, preventing disruptive incidents and fires, and improving overall safety at industrial facilities. Using thermal cameras with AI-powered solutions, manufacturers detect thermal risks in a safer and more accurate way. It allows them to identify overheating early enough to intervene and respond to the problem before it has a major impact on the system.
Stay up to date with all of new stories
Scylla Technologies Inc needs the contact information you provide to us to contact you about our products and services. You may unsubscribe from these communications at any time. For information on how to unsubscribe, as well as our privacy practices and commitment to protecting your privacy, please review our Privacy Policy.
Related materials
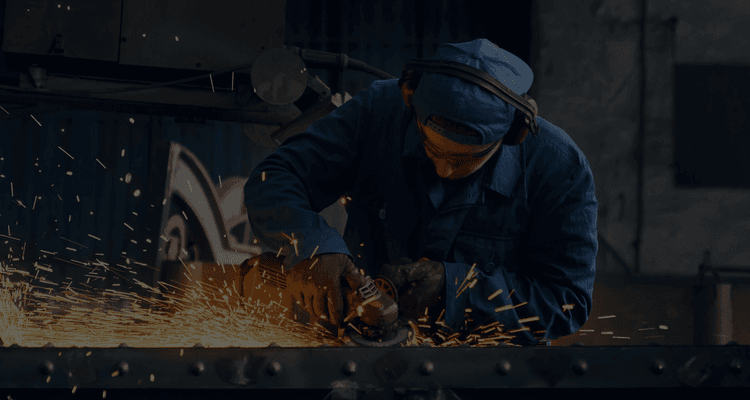
Top Physical Security Trends for Manufacturers to Focus on
With physical security being one of the top concerns for manufacturing units, we are exploring ways how factories and plants could level up their security with AI-powered solutions.
Read more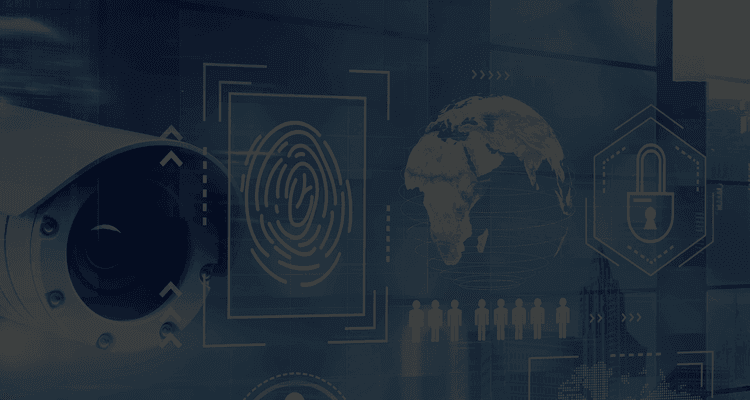
Top Physical Security Trends for 2022
Learn about the top six physical security trends that companies should take into account while rethinking their physical security strategy in 2022.
Read more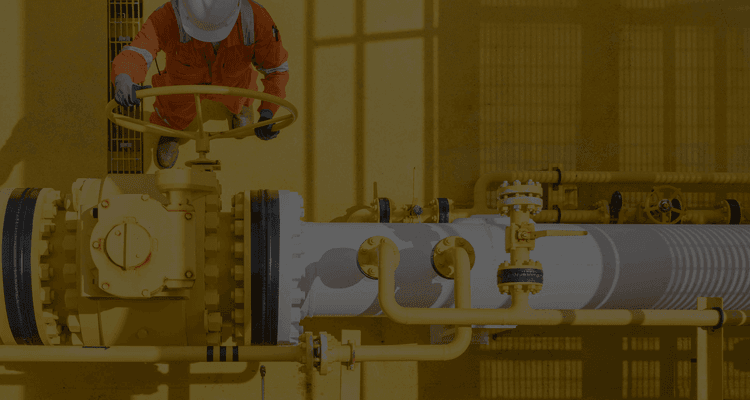
How AI Improves Physical Security in the Oil & Gas Industry
Maintaining the highest levels of safety and control at all times is critical for O&G facilities. Learn how AI helps enhance situational awareness and better protect their assets and workers.
Read more